Many people entering the process industries have no experience or training in the "art" of mixing. Most of what they need to know is not taught in trade schools or in traditional college classes. This knowledge is typically acquired over many years of hands-on experience. Learning, and applying the basics, is a key element in producing successful products.
The High-Speed Disperser (HSD) is the basic tool used by all paint, ink, chemical, plastic and adhesive manufacturers. Although a very simple device, the HSD is often misused or misapplied. The following outlines the basic design parameters of an HSD.
Normal operating viscosity range = 1,000 - 25,000 cps and up to 50,000 cps max Motor specification = 1HP for every 10 gallons of product Disperser blade tip speed = 4800-5200 feet/minute Calculation: Blade diameter x 3.1415 x shaft rpm = tip speed (feet/minute) Disperser blade diameter = 1/3 mixing vessel diameter Disperser blade location: Off bottom = 0.5 blade diameter Under surface = 1.5 blade diameter Batch time at high speed (after last ingredient is added) = 20 minutes Hydraulic lift mounted to allow raising and lowering during operation Portable mix vessels up to 500 gallons
Using these basic design specifications, a mixing vessel can be designed and/or chosen. Many of the mixing problems encountered are directly related to not incorporating these basic design specifications. Using an HSD in a mixing tank or batch that is too large or too small for the HSD will result in poor-quality products or lengthy process times. For example, large HSDs are often used to make small batches such as a 10HP with a 10-inch blade in a 55-gallon drum. The blade diameter to mix tank ratio is almost 2:1 vs. the recommended 3:1. In this case, with a 10-inch diameter disperser blade, tip speeds of 4800-5200 fpm and operating in a 55-gallon drum, a deep vortex would occur, forcing the product upwards and out of the drum.
To offset this problem, many operators will run the HSD at lower speeds, which will not produce the energy and fluid velocity required to create dispersions. Installing a smaller-diameter blade will help reduce the vortex, but the HSD may not be able to produce the faster shaft speed required to reach the 4800-5200 fpm dispersion tip speed. Maintaining the optimum design ratios will help a skilled and experienced disperser operator to produce optimum results.
The primary purpose of the HSD is to incorporate and break down dry agglomerates into a liquid vehicle and effectively "wet" the dry particles to produce a uniform, stable dispersion with the finest particle size possible. To produce the desired dispersion results, the method used to make the batch can be as important as proper design specification and proper formulation.
A typical HSD batch is started with a fairly low level, or volume, of fluid and no dry product. The fluid level may be 50% or less of the final batch. The disperser blade is typically placed on-center and operated at a low speed. The low speed should produce a deep vortex that the dry powder ingredients can be added into. Add the dry ingredients as quickly as the liquid will absorb them. To avoid large, dry lumps from forming, do not bulk load powders. Increase the speed as needed to maintain the vortex as the viscosity increases. Continue to add the dry powders and other fluid ingredients as required. Please note that the disperser blade may be located off-center to reduce the vortex if required. Reducing the vortex will also reduce the amount of air that will be incorporated into the batch. This is especially important in water-based products.
When all of the dry ingredients have been added, you may need to scrape the side walls of the mixing vessel to remove dry materials that may have gathered along the surface of the fluid. You may also need to scrape the disperser shaft for the same reason.
At this point you are ready to run the disperser at its high speed (4800-5200 fpm) for a period of approximately 20 minutes. The disperser can be raised and lowered to eliminate "stratification" or possible layering within the batch.
After 20 minutes, a sample from the batch should be checked for "fineness of grind" using a Hegman, Micron or NPIRI drawdown gauge. Running the HSD at high speed for periods longer than 20 minutes most likely will not produce improved results. The batch temperature will also increase greatly, which may not be good for the formulation. Higher temperatures will evaporate solvents, wetting agents or other volatile components, which may damage the product and increase the percentage of solids. To avoid high batch temperature, the mixing vessel may be constructed with a heating/cooling jacket to control the temperature
If the mix vessel, blade ratios and tip speeds are correct and proper results are not achieved near the 20-minute batch time, the formulation may require adjustment, or a secondary or alternative process may be required
An alternative may be a batch-style rotor-stator high-shear mixer. A secondary process could be an in-line rotor-stator high-shear mixer or, for very difficult-to-disperse products, a media mill can be used. Future articles will discuss these mixers in greater detail.
As a supplier and designer of specialist mixing equipment, Valleyview is proud to have been involved in building and supplying complete chemical processing and mixing plants.You can rely on our team of engineers and consultants, both permanent and on contract, to provide you with the best solutions for your mixing applications. With years of experience, Valleyview continues to supply local and regional clients with excellent products and exceptional service.
In industrial process engineering, mixing is a unit operation that involves manipulation of a heterogeneous physical system with the intent to make it more homogeneous. Familiar examples include pumping of the water in a swimming pool to homogenize the water temperature, and the stirring of pancake batter to eliminate lumps (deagglomeration). Mixing is performed to allow heat and/or mass transfer to occur between one or more streams, components or phases. Modern industrial processing almost always involves some form of mixing.
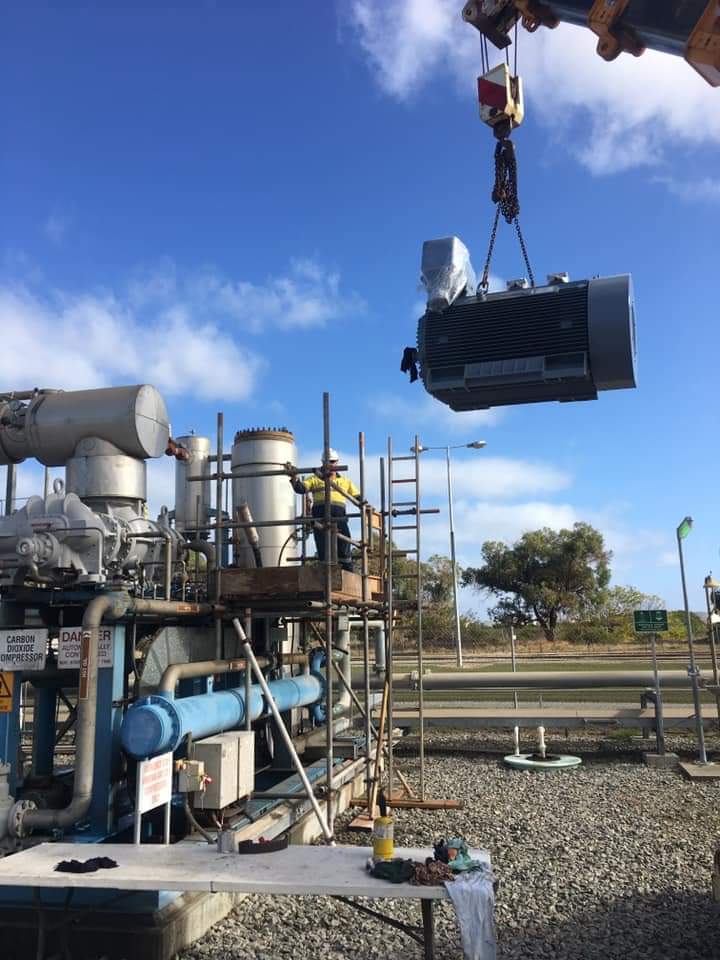
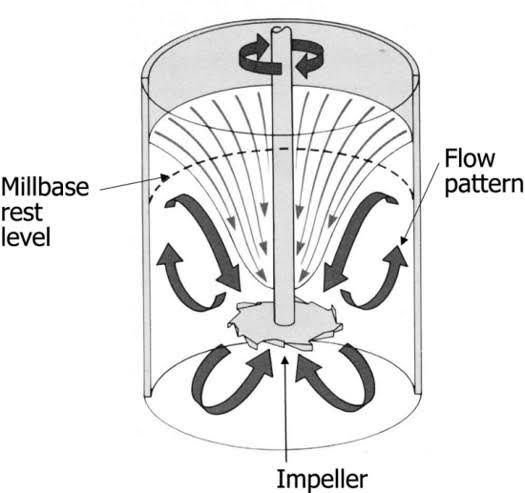

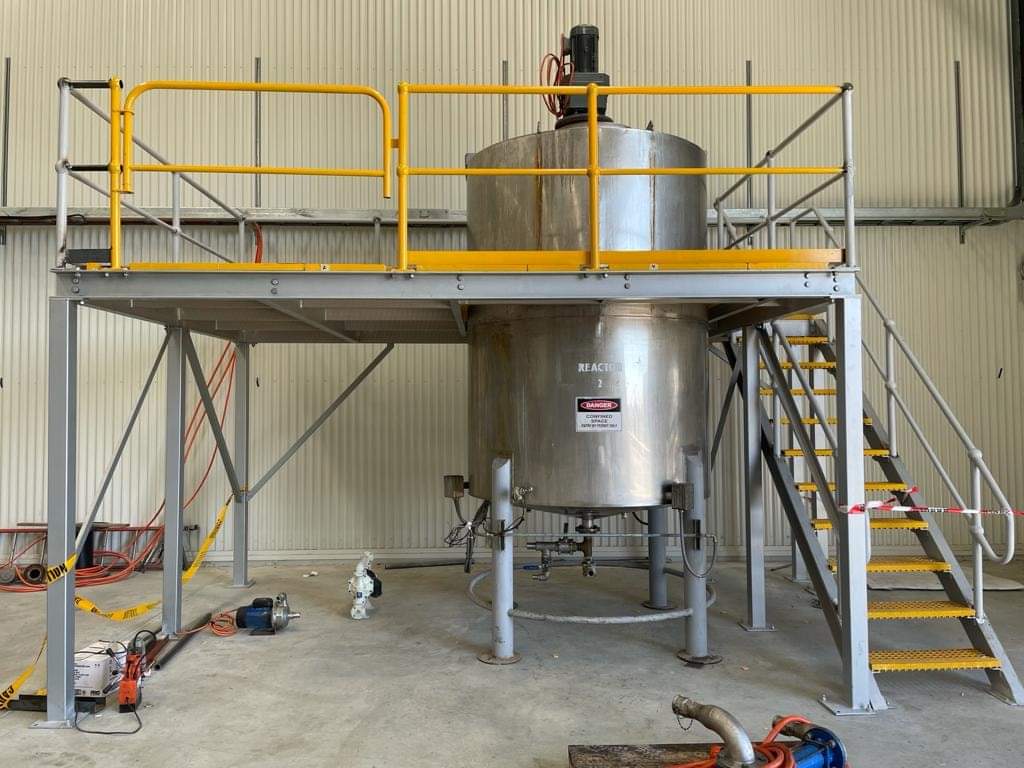
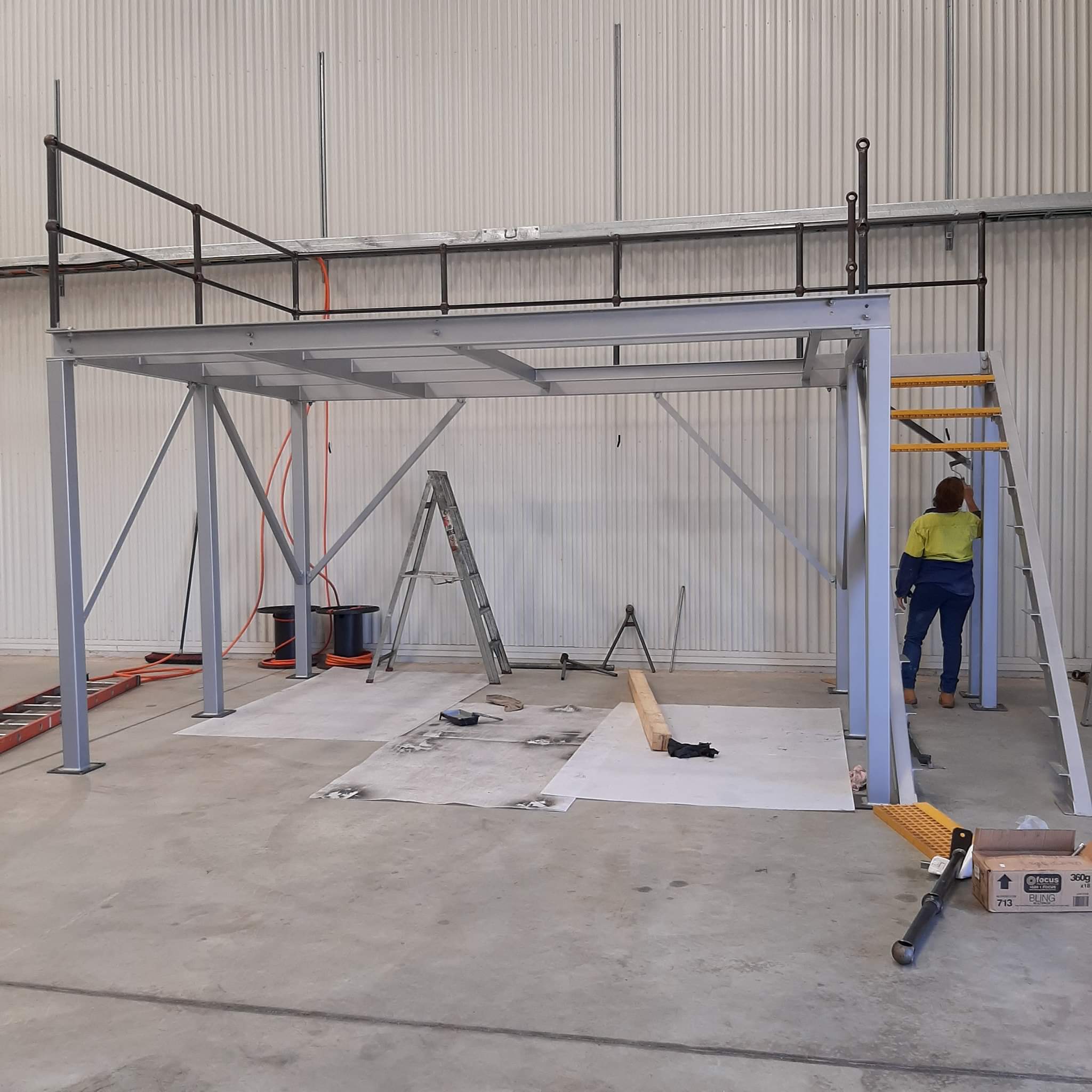